16
Feb
Write On! – What’s a Finish: The Processes We Use on Our Pens
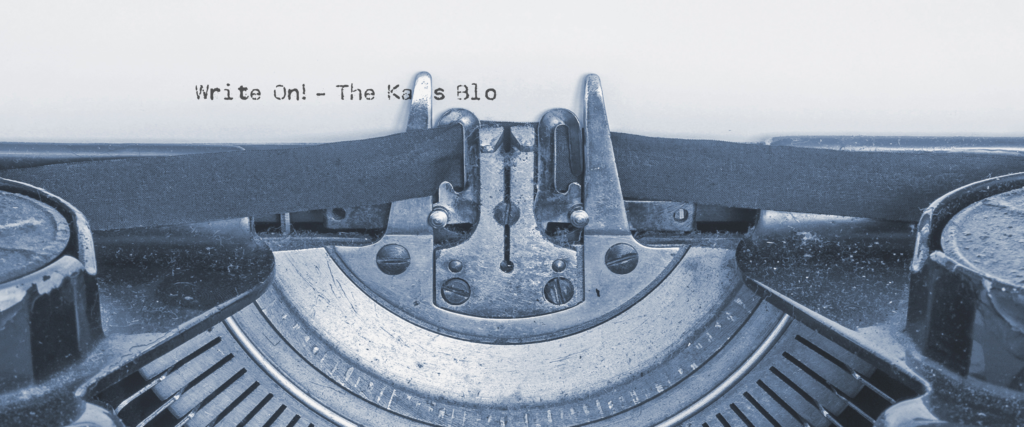
We get a LOT of questions about the specifics of our material finishes, enough that it's become a topic we address in a lot of our digital content. We have a short section on our Frequently Asked Questions that cover it, we've done videos about it, and numerous newsletters have included segments breaking down the materials used and the finish on each material. We'll cover materials and treatments in other blog posts, today I'm only talking about finish. What's the difference between a finish and a treatment? Internally, we define a finish as a process applied in-house to a pen that gives it a unique "finished" look. A treatment is a finishing process completed by an outside, third party, we'll be better about ensuring we're using the proper terminology going forward; examples of treatments are anodize, Cerakote, custom paint, engraving, urushi, etc. We have applied treatments in-house in the past, but that is something that we've gotten away from as it is time-consuming and something an expert should be doing. But on to the meat of the matter, our finishing processes and how we landed on them.
For ease of communication, I'm going to talk about our pens and the materials we use on those rather than discuss pen holders, Speedsters, and legacy products. We use a wider variety of materials on our pens than we do on other products, and most of the finishes translate across to those other products. If you're an old-timer and remember our first Kickstarter campaign for the Render K, you know that we launched that campaign with three materials: aluminum, brass, and copper, and only one finish: raw. A large portion of our first three pens were sold in a "raw" finish. For the raw finished pens these came off the machines, were cleaned, and inspected. The brass and copper pens were then polished, while the aluminum pens were assembled, bagged, and shipped. If you're familiar with raw aluminum, it is very prone to scratching; even just rubbing against denim in a pocket can change the surface and leave scratches or whorls on the body. Copper, while soft, requires more impact or significant friction against a hard object to scratch, so the raw polished finish lasts significantly longer. Brass is the hardest of the three on the Brinell hardness scale, and in it's raw form doesn't scratch or ding easily; this makes it a great option for a raw polished pen.
Unfortunately, the raw aluminum finish doesn't look good over time, it inevitably starts to have wear patterns that overlap, look muddied, and begins to leave black residue on fingers and clothes. Our pens are made to last lifetimes, and we wanted them to still look good decades later. For that reason, we wanted to eliminate the raw aluminum version and replace it with a clear anodized version that would mimic polished aluminum. But we still had enough people who preferred a raw aluminum options, so we began experimenting with finishing options for those pens. Many companies sandblast their pens, and we tried that but found it required a lot of additional cleaning and handwork to ensure all of the sand was out of the pen before we shipped them out. Inevitably, some of the sandblasted pens would have some sand in the body threads and we'd be unable to take them apart forcing us to scrap them. The other option was using a large mechanical tumbler with ceramic media to create a surface finish of variegated marks that softened the look and feel of the raw aluminum and wouldn't change much over time. We adopted this tumbled finish because it provides a raw, durable finish that looks better over time rather than the previous raw aluminum option which ended up looking worse over time.
Traditionally, our raw, polished brass and copper pens were the premium examples of our metal pens. Painstakingly inspected, lightly sanded, then put through a two-step polishing process that shines and then protects the raw bodies; the finished product in both brass and copper shined with luster and looked amazing. Rather than seal the pens in an attempt to keep them bright and shiny, we leave them raw and let the customer decide whether to continue to keep them polished or let them patina over time. One of the big draws of brass and especially copper is the fact that over time the surface will oxidize. In brass, the patina mutes some of the brilliance and then brings out the yellow of the material; if given a long enough time the brass will darken to a brownish black, though that often takes decades and requires some form of surface moisture. Copper, on the other hand, will start to patina in a few weeks, faster if it's handled a lot. The bright copper color will deepen to a rich pinkish-brown before taking on an almost brown leather-like color that even "looks" soft. In wet environments if the pen is left with moisture on the surface for long periods of time, whitish, green spot can appear in those areas. If a patinated finish is not for you, use of a jewelers cloth can keep the finish of your brass or copper pen bright and shiny.
When we began expanding the use of Delrin for our pens, we knew that we'd have to come up with some finishing options for those pens. Delrin has a tendency to scratch easily, even a sharp fingernail can put a pretty deep scratch on Delrin, and black Delrin is prone to highlighting even the smallest scratch. White Delrin, on the other hand, does a wonderful job of hiding surface marks. One of the nicest things about this material as a whole, is that it machines relatively easy. The finished product comes off the machines with a wonderful finish, and we've always wanted to keep that raw, machined finish whenever possible. Most of our white Delrin pens have been sold with that raw, machined finish. A small batch of Vertex pens and Decograph pens in white Delrin were sold with a tumbled finish, but those were mostly done as an experiment to see what the finished material would look and feel like. For black Delrin, the opposite is true. 90% of our black Delrin pens are sold with a tumbled finish, and the other 10% are sold in a raw, machined finish. Our use of raw, machined black Delrin pens has expanded recently because our newer machines and processes have improved the finished product, but we still think the tumbled black Delrin looks and feels better than the raw black Delrin.
For our Acrylic and resin fountain pens, we've used a variety of finishing techniques; from hand-polishing to a multi-step process with numerous liquids and bars used to provide the perfect finish. No two resins polish the same, if the chemical makeup of the resin differs then the process has to adjusted, but we've gotten much better about narrowing the process to the easiest and most repeatable process possible. We currently use a multi-step method that starts with wet-sanding each piece, then use a two-step liquid polishing compound, followed by a two-step soft wheel process with a dry compound on the first wheel, and we finish it off with a hand polishing step to make sure the finish is perfect. It's time-consuming, but ultimately provides the best looking finish for these materials that we've been able to accomplish. There are only a few matte finished resin pens in existence that we've sent out, and that's not likely to change any time soon. While we like that look, it's not a look we plan on doing in large quantities.
Those are the majority of finish options we have on pens that are currently available or will continue to be available in the future. We continue to experiment with finishes that are outside of those listed above, but inevitably, our current selection of finishes ends up being the best options for our pens. That's not to say we won't release some other options in the future. We ended up releasing the first 20 Decograph pens that came off the machines in a raw aluminum finish as a throwback to our early days. We still have customers who ask us for the raw aluminum version because they're collecting a full set of our pens in that finish. If we expand to more materials we might be forced to adopt other methods of finishing our pens. We don't always decide on the easiest, fastest method of finishing our pens; the goal is that we have the best looking product with most amount of efficiency. If that requires a multi-step process conducted by a person, that's what we'll do. If we can take a part off the machines and have it look and feel perfect, like one of the batches of Ultem Modals we have coming up, that's also perfect. Funnily enough, where finishes are concerned, we're never finished trying to options, but our current options are the ones we feel show off our pens in the best fashion.