25
Apr
Write On! – How Are Metal Pens Made?
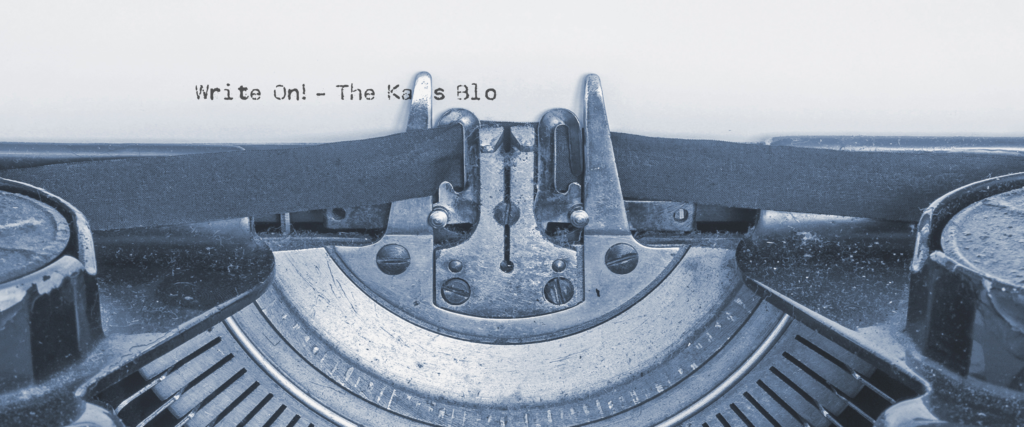
"How are your metal pens made" is a question we get asked in emails and in person quite frequently. Surprisingly, the answer isn’t as straightforward as you’d think. There isn’t just one way to make a metal pen, and the actual production process changes quite a bit based on the design of the pen itself. Some metal pens are designed to be made in such large quantities that they primarily rely on techniques like deep drawing or stamping to create the majority of the components. Other designs are simplistic enough that they use major components made out of precut tubing that only require minimal machining and a few smaller parts that have more intricate machining to complete the pen. Then there are designs where the majority of the pen is machined from a solid bar of metal and the small fixtures or hardware are made via stamping or sourced from off-the-shelf options. The final type of metal pen are those that are made in very small quantities and are made up almost entirely of machined or hand made components. There are markets for all of these types of metal pens, and there are producers of all of these types of pens. We fall into the category of manufacturing the majority of our pens via machining and using stamped clips and off-the-shelf screws for the majority of our pens.
Another aspect metal pen manufacturers have to consider when it comes to machining or making a metal pen, is the material chosen for the pen. Common materials for metal pens include: aluminum, brass, copper, stainless steel, and titanium; and while those are all very similar, they can be made in many different ways. Aluminum, brass, copper, and stainless steel CAN be deep drawn into different basic shapes. Brass and copper can be formed via other methods as well that are then adapted in the pen making process. Pens from titanium can be machined fully from bar stock or utilize titanium tubing. The design and the material choice are the two big factors in identifying how the product was made.
Let’s take a look at a few of our pen designs and explain how those designs impact our manufacturing process. For this exercise we’ll look at the Retrakt and Modal, but keep in mind we are a machine shop that leans toward designs we can produce on our own CNC machines.
The Retrakt consists of a two-piece body design, a simple stamped clip design, and an off-the-shelf click mechanism. The main components, upper and lower body, were designed by us to be our take on a traditional ballpoint pen style. The decision to have the pen feature a two-piece body was partly due to the machines we owned at the time and an homage to traditional two-piece click pens that unscrewed in the center of the pen. We designed the clip to be very durable but made out of stamped stainless steel because that is easy to source from a local stamping company we had an existing relationship with. An existing click mechanism sourced from the German manufacturer, Schmidt, was chosen because it provided very good value and quality for a product of this type in 2012. Similarly, we sourced off-the-shelf fasteners to keep cost down but sourced them from a company known for stocking quality parts.
Alternatively, the Modal was designed with a mindset of keeping as much of the pen in-house as possible. We wanted to control the manufacturing on the pen body, but also on the mechanism and the clip. This allows us to prototype and futureproof the product through as many iterations as possible for a much lower amount of capital. The Modal relies on both our CNC Swiss lathes and CNC mills for production. It has five fully-machined parts including a two-piece body, an internal slider, an actuation knob, and a mill clip. It went through three separate design iterations, and two different engineering iterations before we sold the first batch. Being that we control the production of almost the entire pen, it has undergone two more engineering iterations since we sold those first batches of pens. These engineering changes were to strengthen the design and manufacture it faster. We could not have done that if we were reliant on outside processes and parts.
Those are how the majority of our metal pens are made. We machine as much as possible in-house, and source as close to our shop as we can for parts that we cannot make. Other companies take different approaches to how they make metal pens, and how they market those metal pens. Which is one of the reasons we get asked how we make our pens. There are two final steps that are a part of making metal pens: finishing and assembling.
The finishing process for metal pens is more varied than the material selection process. Metal pens can be anodized, painted, engraved, laser-etched, machine detailed, stamped, formed, blasted, dipped, dyed, polished, electro-chemically treated, aged, and that’s only a few of the finishes commonly seen on metal pens. We tend to only use anodize, Cerakote (paint), and tumbling as the finishes provided on our pens. This simplifies the processes but also provides the best options for fully-machined pens. How the pen is actually manufactured can dictate how it's finished, as well as the final price point plays into the finishing process quite a bit.
Finally, the assembly of the pen can be very simple to extremely labour intensive. There are some pens that can be put together en masse with large machines that basically press fit all the parts in one movement. This is large-scale production at its finest, and mostly is done on drawn or stamped pens. For a manufacturing company like Karas Pen Co, we rely on hand assembly by a technician. This job is done by manually assembling all of the pieces with tools or by hand. Some of the more custom metal pens include small placement of jewels, buttons, or other handmade components that require incredible skill to complete. Each pen can have hours of assembly that are required before the pen is even tested for functionality. That kind of product brings a premium price point.
We’re not a tiny company, though we have a small staff. We fall into that middle-ground category of machining at a decent-sized scale of production for the type of product we design and manufacture. It’s sustainable for us with our current staff, and we can easily scale up or down depending on demand, which is something we’ve done throughout our decade-plus time making pens. Not every metal pen is designed or made the same. Even the “how it’s made” aspect doesn’t communicate the overall quality of the product. We like to answer the unspoken question of “how does the manufacturing process impact the quality” by providing an extra level of transparency. Put simply, we just tell you how we make it and where it’s made, and if we don’t make it, we tell you where we get it from. Then to top it all off, we give you a lifetime warranty so you don’t have to worry about it. That’s the final step of “how metal pens are made”, they’re made with a guarantee of quality that they’re made to last a lifetime.
Comments (3)
I need to start making the Modal in titanium please!
I need to start making the Modal in titanium please!
I need to start making the Modal in titanium please!